PILOT CASE
VDL Weweler:
Trailing arm production process demonstrator
In order to overcome identified challenges within the VDL Weweler trailing arm production process this industrial pilot envisages the use of several non-destructive inspection methods and a Digital Twin model of the production process. To keep track of the important production parameters, in real-time, and with the support of AI modules to identify anomalies and adjust the production parameters accordingly.
The proposed approach will allow to adjust the production process to deviations or abnormal patterns ensuring the production of high-quality products while enabling a zero-defect manufacturing process
Pilot Description
The use of digital solutions as well as non-destructive inspection methods for reducing defects are envisioned within the existing production process. The use of an x-ray scanner, various laser triangulation measurements, thermographic imaging, vision camera inspection and 3D scanning are part of the project. The creation of a digital twin model is targeted for modelling the key steps that may determine or impact the key defects of the trailing arm production process. A number of sensors is to be included in several steps which along with machine parameters and existing in-line measurements will deliver the digital input to the digital twin model.
The digital twin model will include one or more intelligent mechanisms to analyse the incoming data and determining the ideal configuration of machine parameters for ensuring the proper quality of the resulting products. Thus, the introduction of several inspection systems in combination with the envisioned digital twin model will enable the dynamic control of the process parameters of several machines based on the inspection data.
Expected Goals
- Gaining more insight into the combined factors that play a role in the occurrence of defects in the products. To then determine to what extent these factors have an influence so that the appropriate actions can be taken. A direct annual waste reduction of 16,2% is expected, downtime is expected to be reduced by 2,2%.
- Automating the measurement of critical dimensional properties and detection of surface defects will eliminate manual actions. The result is an expected annual 790 hours saved in several parts of the production area.
Problem definition
By developing and taking into use unique innovative production methods, as an organisation, you are entering an unknown area where many things still need to be discovered. Because of this and the drive of the organisation to continuously improve, new challenges always arise.
Despite the high degree of automation and far-reaching developments, defects can still occur in the production process. Defects that result in wastage in the form of corrective measures, wasted material and time.
In order to remain competitive as a production company and to guarantee the maximum added value for our customers, it is crucial to prevent any form of waste, in this case within the production process.
Identified challenges
- Due to the large amount of factors that can influence various possible defects, analysing problems and identifying root causes is a complex process. In order to carry out this process efficiently and effectively, the challenges lie in collecting the correct data and processing this data in such a way that the right connections are made to further optimise the production process.
- In addition, with any changes that are made, the existing production process must continue to meet all strict requirements in order to be able to deliver a continuously high level of quality.
Impact from openZDM technologies
The expected impact of various open ZDM technologies to be implemented include reduction of defective products, downtime and elimination of sorting and manual checks.
In addition, the technologies can make a major contribution to achieving first time right in future developments.
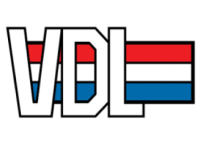
Leading company
VDL Weweler is a leading international designer and manufacturer of (customer specific) air suspension solutions for trailers, trucks, and buses. VDL Weweler develops, produces, tests, and sells air suspension systems, axle lift systems and parabolic springs from its high-tech plant in Apeldoorn (Netherlands). With its unique production, housing one-off machinery, advanced robotics, state-of-the-art test facility, optimum logistics and world-class craftsmanship, VDL Weweler can offer its customers the added-value they require. Using the very latest in 3D design and rolling & forming technology, VDL Weweler creates very strong but cost-effective and lean flexible trailing arms.