PILOT CASE
Vidrala:
Bottle manufacturing demonstrator
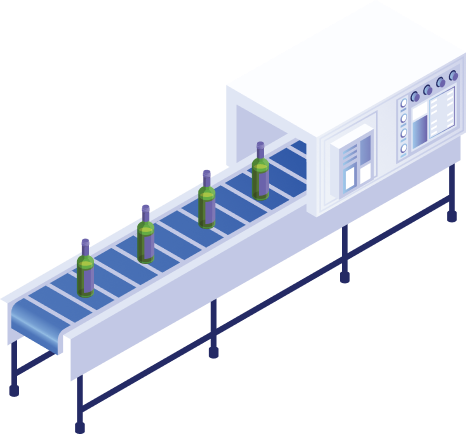
Pilot Description
Vidrala manufactures glass containers through a continuous process involving the melting of glass. This molten glass is brought through some forehearths to a spout, where some glass gobs are cut. These glass gobs will be formed into a bottle or jar each, without any addition or subtraction of mass. The conditions in which these gobs are formed depend on the temperature and homogeneity of the glass and will affect the regularity of the thickness of the bottle’s walls.
This relationship is not obvious. Some experience is held inside the factories, and some shapes are regarded as better than others, but this knowledge is qualitative and very difficult to optimise. In the first use case of Vidrala, the usage of modern data science tools should define the actual limits for the gob shape and the impacts of those limits.
Expected Goals
- Develop a gob shape control system and a thickness measurement predictor
Problem definition
Identified challenges
- The first challenge is the correct collection of data. The amount of suppliers and types of equipment involved requires a deep understanding and development of data tools.
- The second is defining the fine line that will make the balance between statistical significance, measurement errors, limits, and random variation.
Impact from openZDM technologies
